What Is Sand Casting?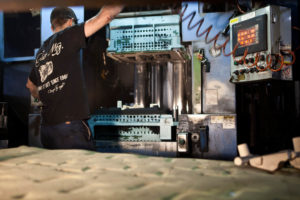
Sand casting is a method of producing metal pieces from a mold made of tightly packed and bonded “sand.” While it’s helpful, at a high level, to think of this sand as the kind you might find along a shoreline, this material is made of several components. The primary component is a fine, silica-based particulate, along with water and a bonding component typically called clay.
The process works this way:
- A pattern is created for the intended shape.
- The sand is poured, packed and bonded around the pattern to form a cavity (in two halves). It is then joined to form the mold.
- The molten metal material is poured into the mold cavity through one or more runners, which must be formed into the sand mold as the entry point or points for the material.
- The molten metal cools and solidifies.
- The sand mold is broken away and the finished part is removed.
What Are Some of the Pros?
Sand casting, as a process, has several benefits for a wide range of use cases. These include:
- Extremely low tooling cost: Because the sand material can be easily formed into a mold, used, broken and re-used, sand casting has a minimal cost of tooling compared to similar processes.
- Unparalleled part versatility: The limits of sand casting are, in general, only dictated by what type of patterns can be created. Because patterns can be made from a variety of materials (including wood, plastic or metal) and can be intricately detailed, sand casting is suitable for complex pieces as well as simpler forms.
- Short lead times: Lead times for sand casting are very short (in part because of the ease of creating tooling). Do keep in mind that, depending on the finish required, additional machining is often necessary for sand cast parts.
- Suitability for low quantities: Low tooling costs and fast turnaround mean that sand casting is an ideal cost-effective process for small-quantity runs, even as low as a single piece. This makes it useful for prototyping and one-off production.
What Are Some of the Cons?
The nature of sand casting means that while it offers extensive benefits in some areas, there are other applications and requirements for which it is not as well-suited. These include:
- Lower strength: Sand casting is typically not suitable for parts requiring high tensile strength, due to the porosity of the mold. Machining or other types of molding or casting may be better able to produce the necessary density for the part.
- Pattern maintenance: Depending on the number of times a pattern is intended to be used, maintenance and storage may need to be written into your logistics process. Patterns wear over time and, based on the size and shape of the part, might be inconvenient or difficult to store.
- Lower accuracy: Sand casting is not suitable for applications requiring extremely tight tolerances. Again, in these scenarios, conventional machining is typically the more suitable option.
- Rough surface finish: Because of the nature of the sand material, the finished part will have a rough surface finish (typically around 125 RMS). Unless this is suitable for the product, further machining and finishing are almost always required.
Each process that you might consider will have different pros and cons, which will all play a role in helping you decide which process is the right one for you. We hope this article will help you make a well-informed decision by understanding the process of sand casting: what it is, what the potential benefits are, and what any potential drawbacks might be.
For more information about sand casting and to learn why we’ve been leaders in the field since 1966, contact LeClaire Manufacturing today.